Scalable designs
optimal designs for dynamic design requirements
What is a flexible design?
To answer the above question, another one can be asked from a product development point of view:
How do you design a component when the design requirements can change at any moment and without advance notice?
That is the question my dissertation tries to answer. To do so, I came up with design metrics for qualitative descriptions such as flexibility and robustness. I used optimization, automation and machine learning to obtain thousands of possible designs. This is a 1000 fold increase in the number of alternatives that are presented during client meetings in the industry.
A scalability assessment tool
I also developed an online tool to help support decision making and identify scalable designs (a form of flexibility when remanufacturing is an option). The tools relies on machine learning models (as surrogates for physics-based models) to estimate the sensitivity of the design to external changes (loads, specs, etc.) and whether it can be scaled to fulfil said changes.
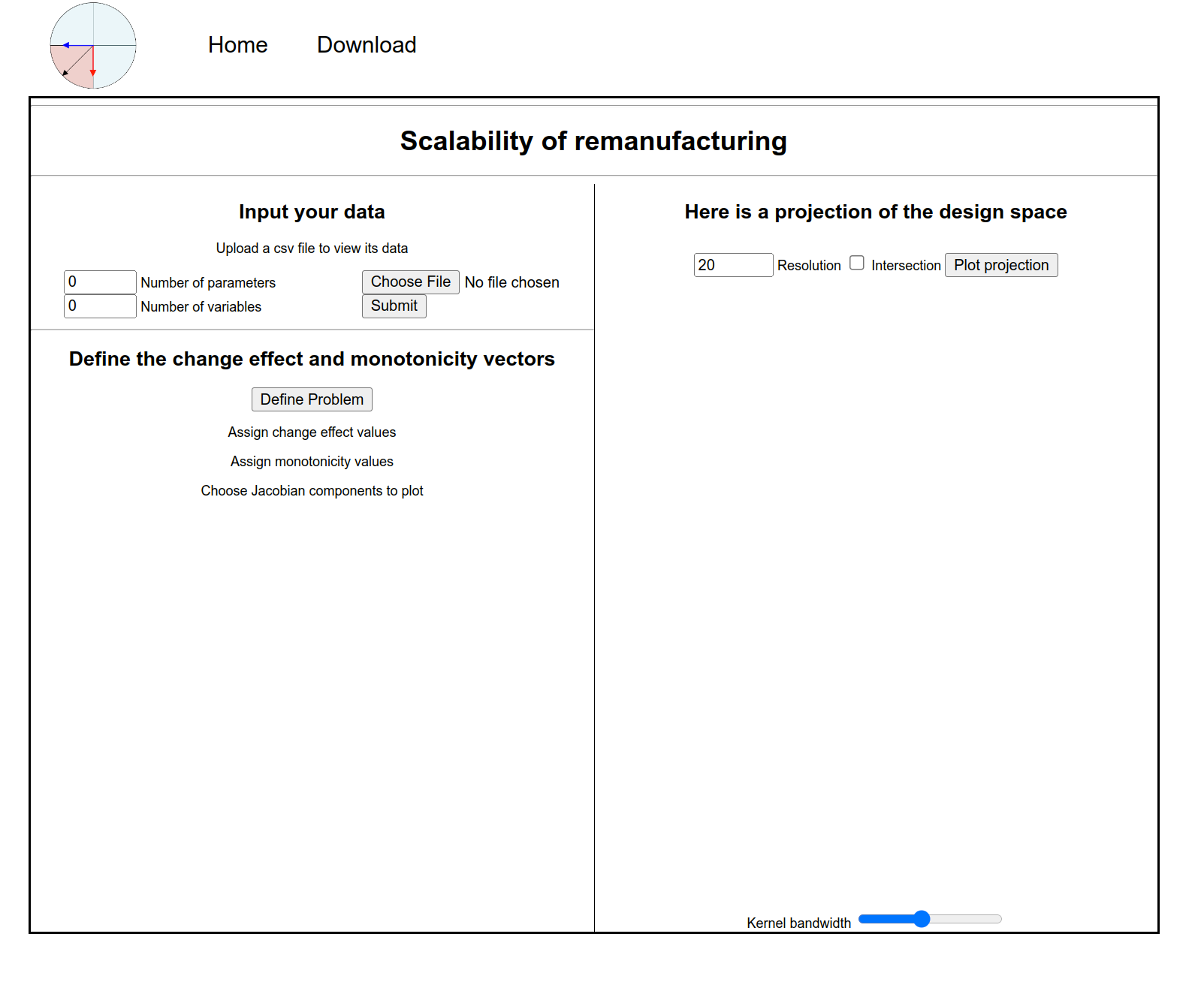
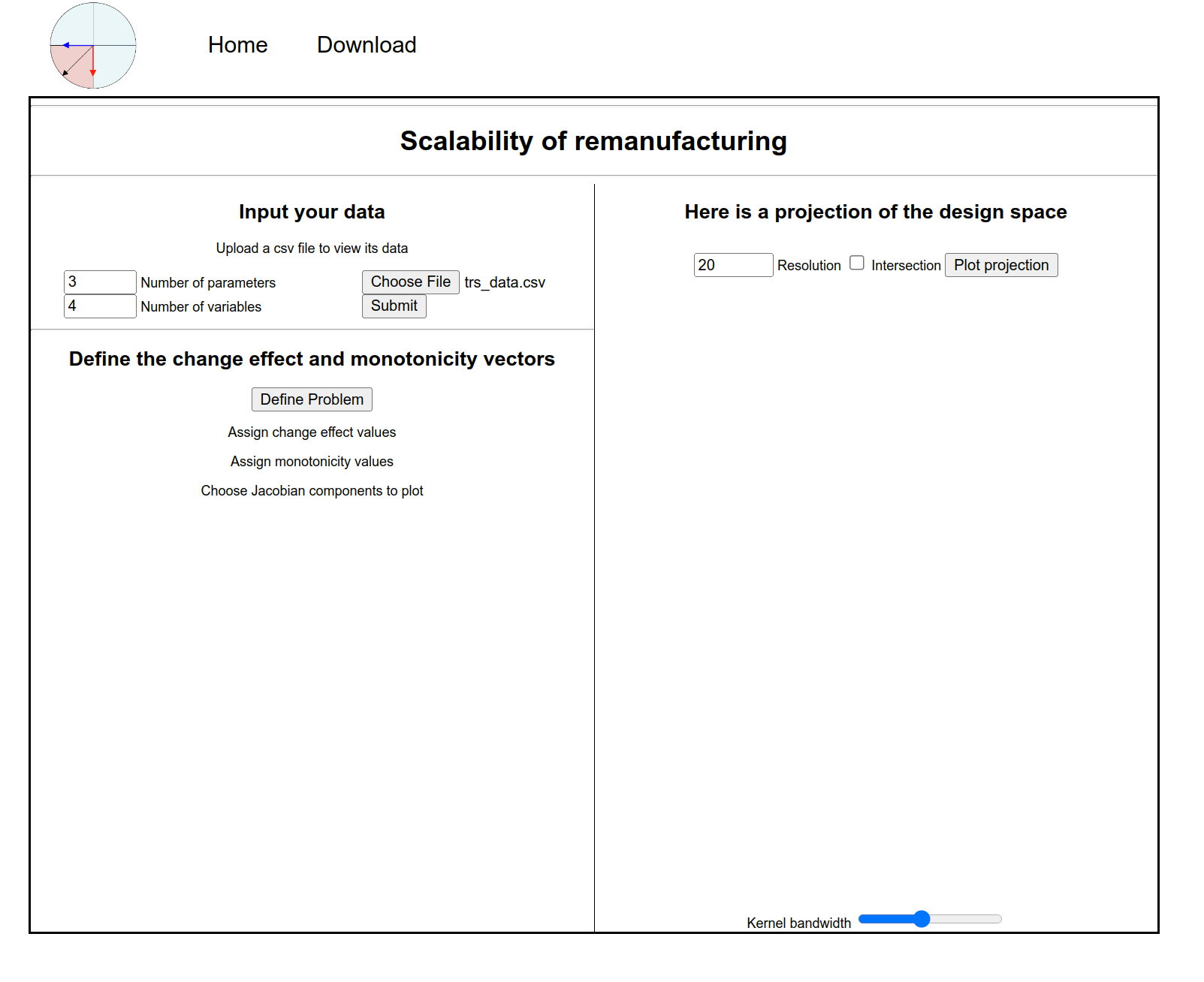
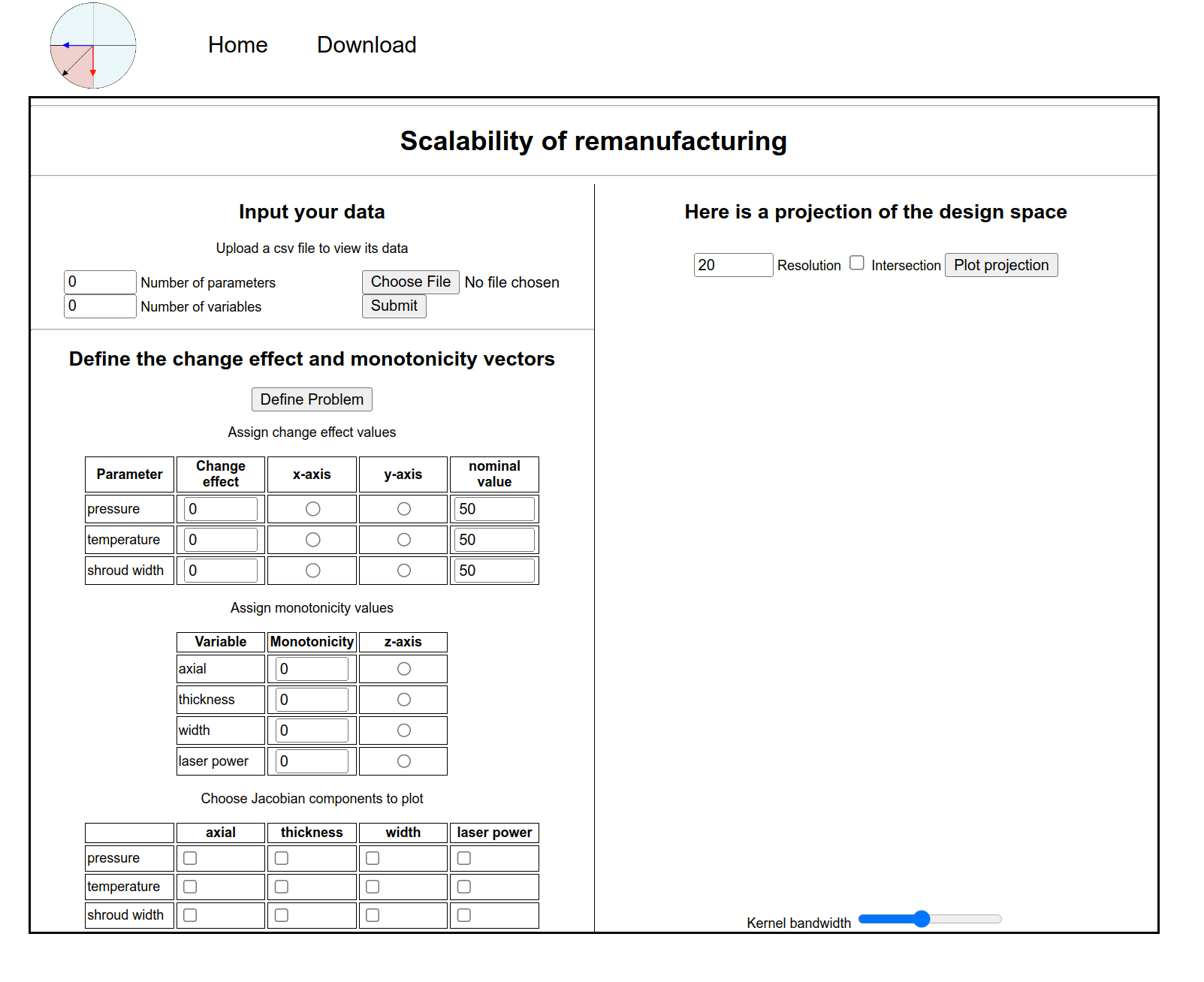
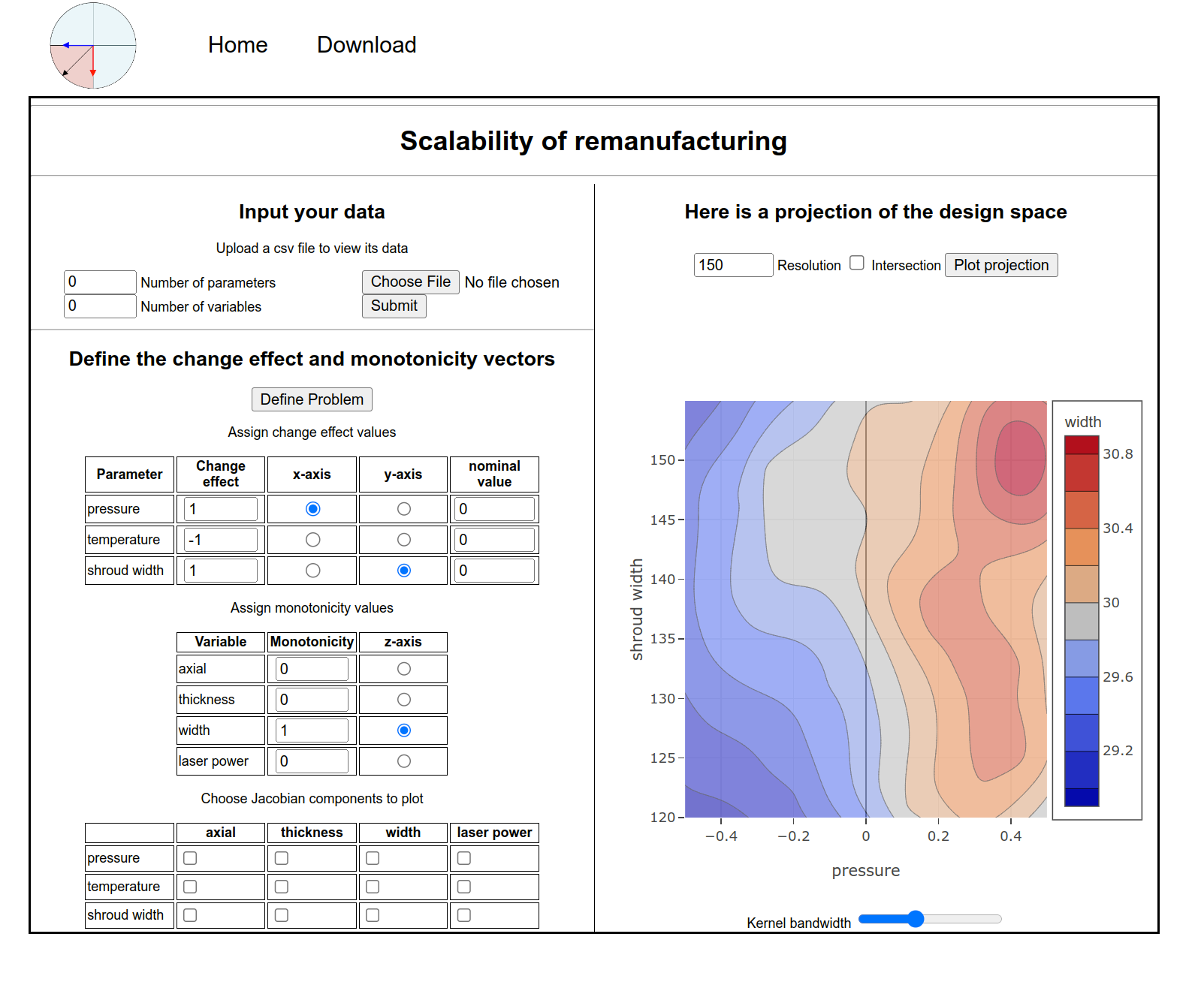
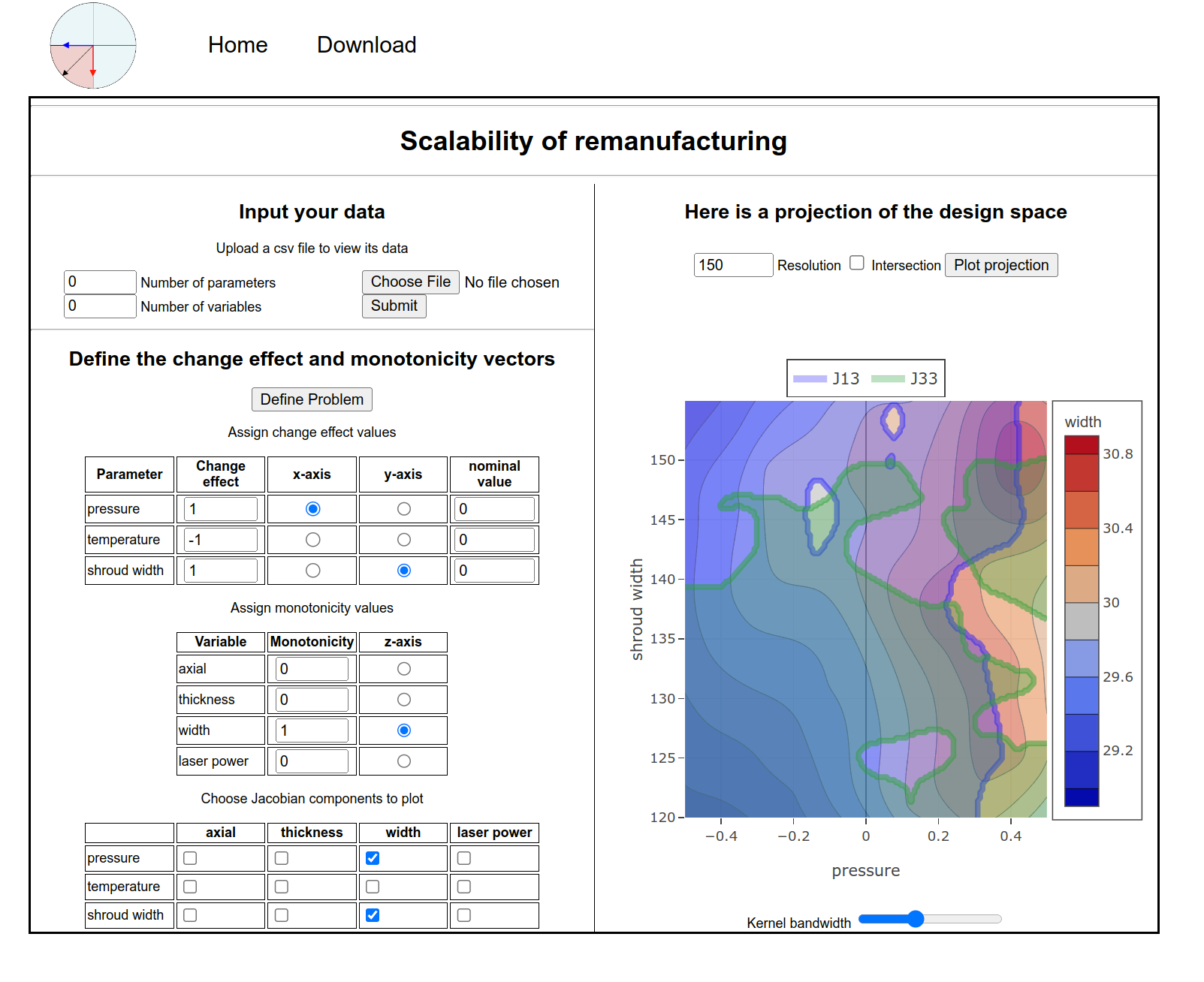
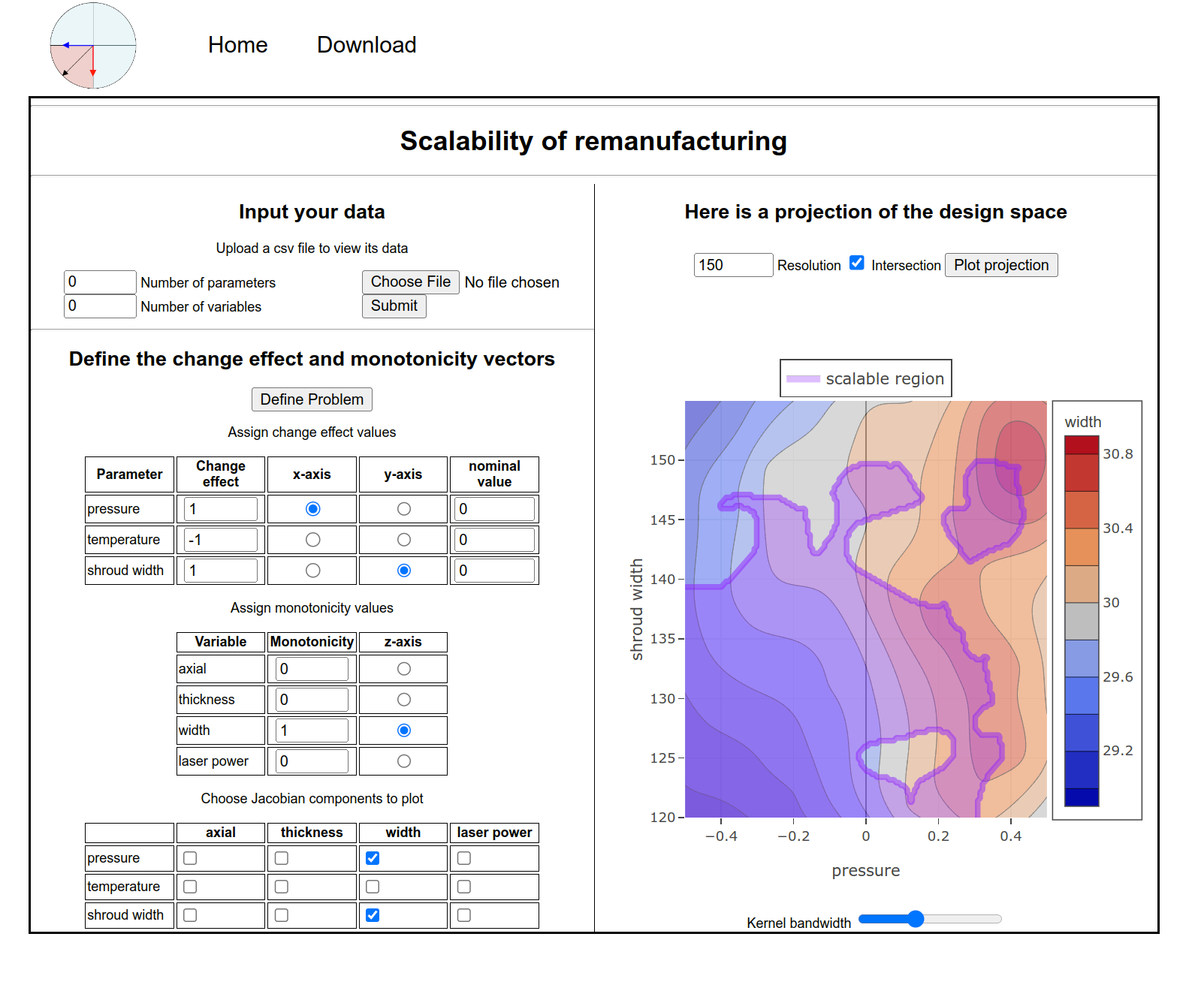
By exploring all these alternatives, potential cost savings can be made over a period of decades.
Solving a remanufacturing problem for GKN Aerospace
I used the previous tools and principles to solve a remanufacturing problem for GKN Aerospace, which is an aeroengine Original Equipment Manufacturer (OEM).
At the time of this project, GKN started investing in additive manufacturing (AM) technology to remanufacture their structural components using directed energy deposition.
I managed to model the remanufacturing process for a turbine rear frame using a moving Gaussian heat source that results in temperature gradients on the surface of the turbine rear frame as shown below. The thermal expansion permanently distorts the structure and is used to study the performance of the remanufactured part when loads are applied during opertion.
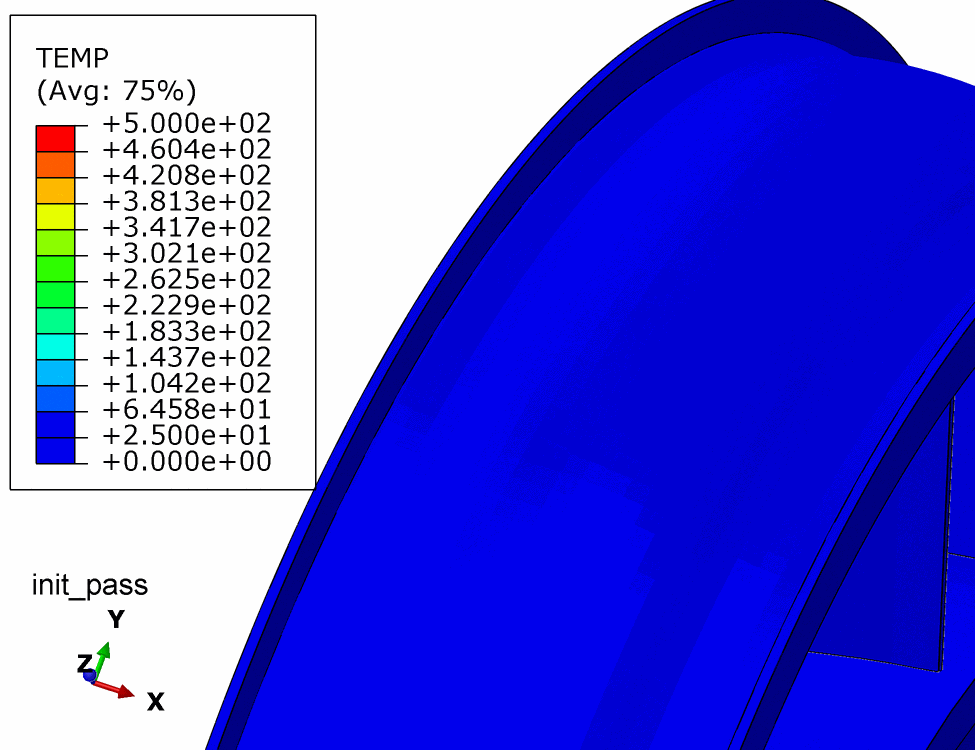
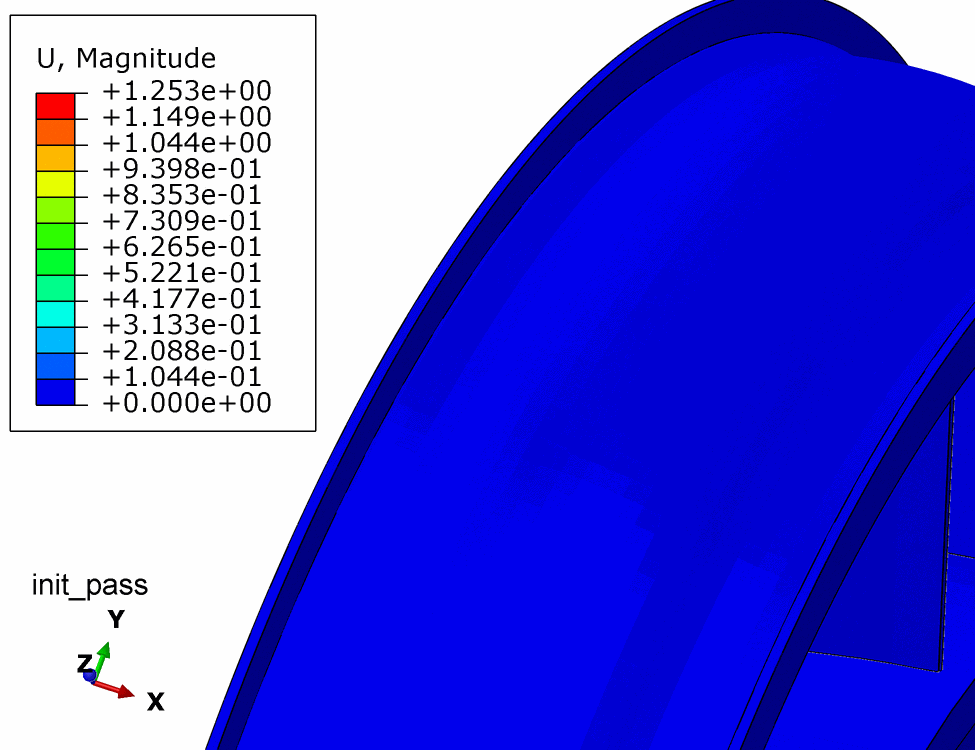
We then investigated various stiffener designs and calculated their scalability using the tools that I developed. We managed to quantify the reliability, performance (given by weight), and flexibility of a various stiffener patterns shown below.
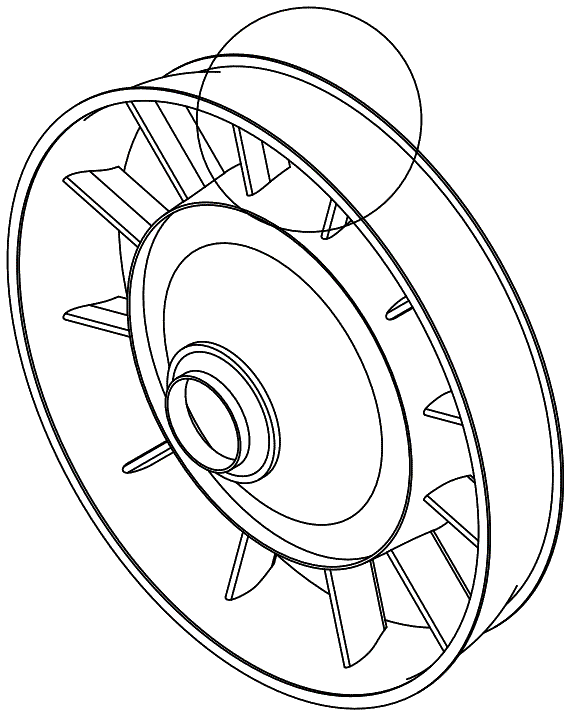
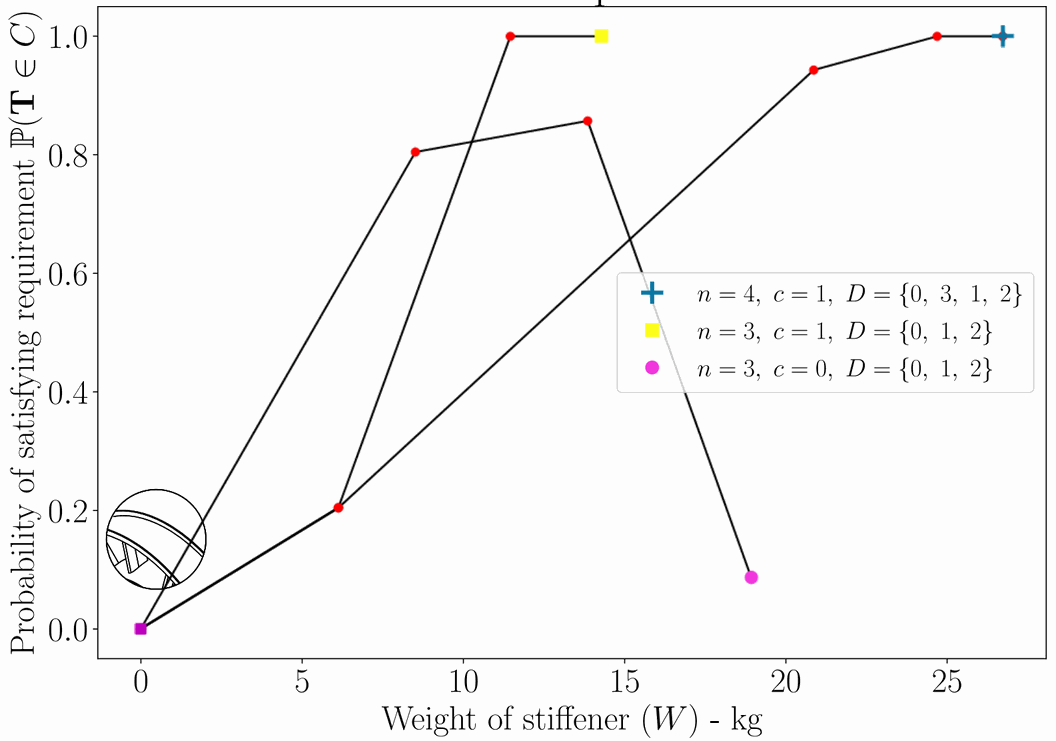
Awards and recognition
My research culminated in a technology transfer at GKN Aerospace Engine Systems so that engineers can go to work, incorporating these algorithms in their workflows and give GKN a competitive edge.
The research also resulted in a best paper award in the ASME Journal of Mechanical Design for 2021. The award was presented at the IDETC-2022 conference in St. Louis, Missouri, USA.
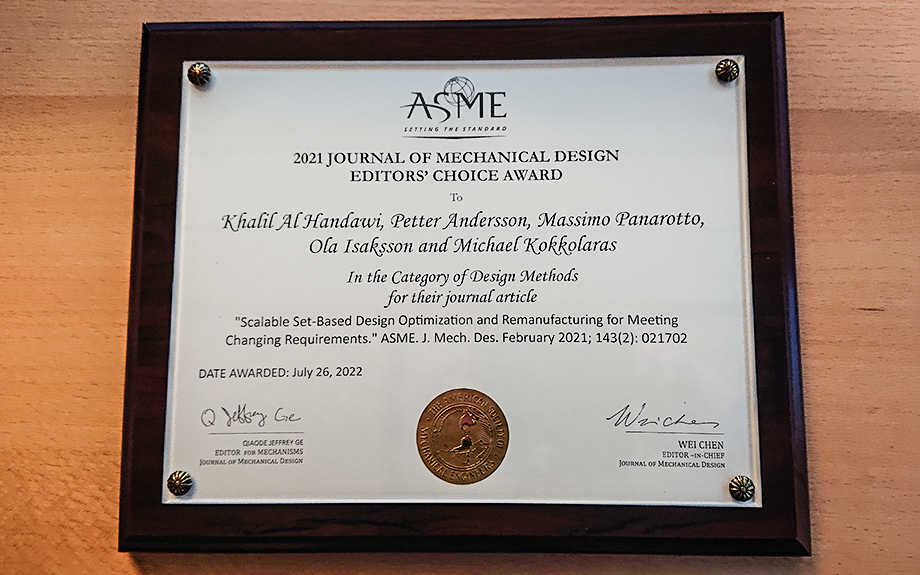